ECDriveS® stands for Electronically Commutated Drive System, a brushless DC gearmotor. But ECDriveS® also stands for “easy drive,” the simple, efficient and cost-cutting drive solution for roller conveyors from SEW‑EURODRIVE.
ECDriveS® is uncomplicated: Just connect and you’re done – “easy drive” indeed
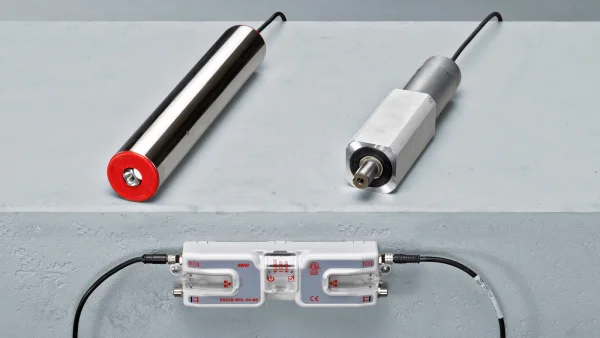
Our ECDriveS® is a DC drive with 40 W continuous power and up to 100 W dynamic power that is optimized for the typical power ranges of roller conveyors used in light-duty materials handling technology. ECDriveS® units are remarkable for not only their ease of use—just connect them and you’re done—but also their adaptability. They are extremely easy to integrate and start up, and once operational they exhibit excellent durability and long service lives.
The ECDriveS® drive system rounds out our broad product portfolio of standard gearmotors, motor starters and decentralized drives for intralogistics in the low power range.
Consult our sales team.
Your benefits
-
Save time
You can easily order the drive system, the driven roller and the gearmotor from just a single supplier: SEW-EURODRIVE. -
More than a market standard
ECDriveS® offers higher performance and overload capacity than comparable solutions. -
Implement positioning tasks easily
With the integrated encoder in ECDriveS®. -
Your choice of control options
Centralized control via a PLC or decentralized, intelligent handling logic for zero pressure accumulation and much more. -
Future-proof networking
With Ethernet.
Characteristics
- Our ECDriveS® units are drives with 40 W continuous power and more than 250% overload capacity. They combine a sturdy planetary gear unit, which is supported on both ends, and an efficient permanent magnet motor (BLDC).
- The integrated encoder allows for precise speed control, and controlled brake ramps let you position the material precisely and independent of the load.
- A thermistor is implemented to protect the motor, meaning you always know the current motor temperature.
- An electronic nameplate allows you to set up the drives automatically. No other system is this simple and easy. The motor can be controlled via PROFINET IO, Ethernet IP, Modbus TCP, EtherCAT® or with binary control. I/O modules can be used to expand the drive system.
Technical data
Areas of application
The units are suitable for all light-duty handling tasks with S1 operation and up to 40 W.
Example: zero pressure accumulation
Example: positioning of material to be conveyed